After 40 years, Jon Ashton of Ashton Surf Designs is widely regarded as one of the premier surfboard shapers on the East Coast
Written by Kristen Hampshire | Photography by Pamela Aquilani
Most commercial surfboards are produced on a machine using a computer-based CNC machine — the equipment you’d find in many factories — which can swiftly cut the shape and prepare a board within 30 minutes. But custom boards like the ones Jon Ashton creates are of an entirely different scope.
“There aren’t too many shapers out there who do it by hand,” he said, sharing how he started the craft while in high school. Living in California, he surfed the days away and earned money to make his boards by collecting and turning in old Coke bottles. When his board wore out, he gathered the materials to fix it himself.
Today, Ashton is one of the most respected surfboard shapers on the East Coast, and he has completed more than 10,000 boards in his 40-year career. The owner of Ashton Surf Designs in Berlin, he moved to the Delmarva Peninsula in 1980. “And to my surprise, there wasn’t anybody building boards in this area,” he said.
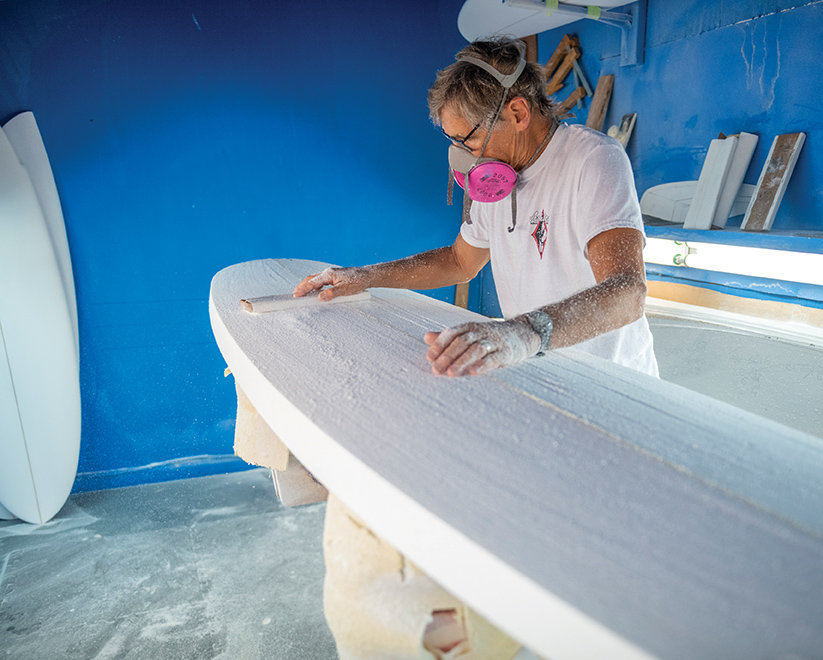
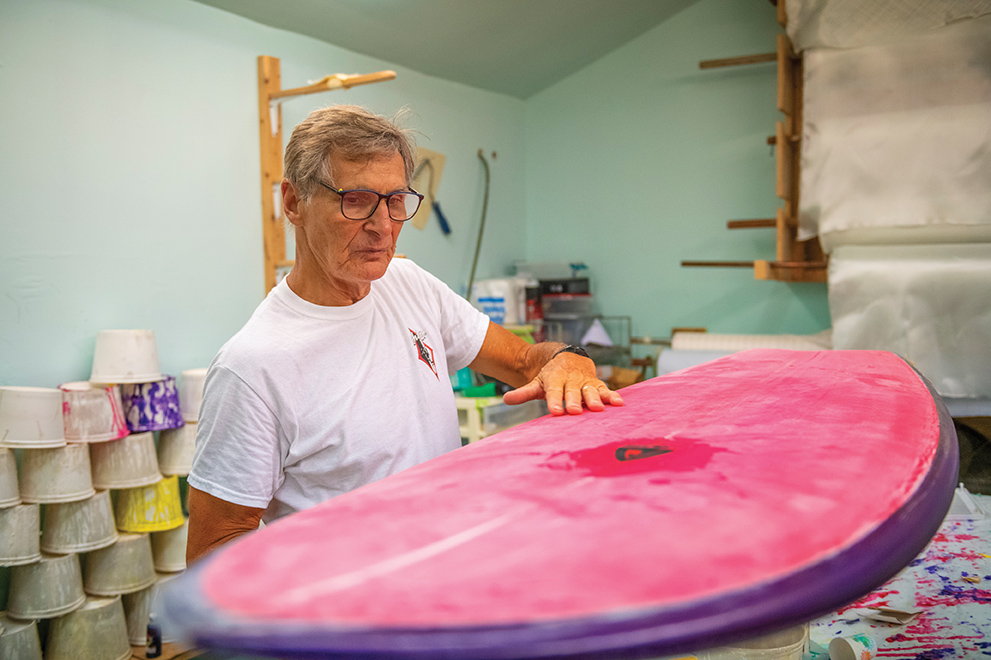
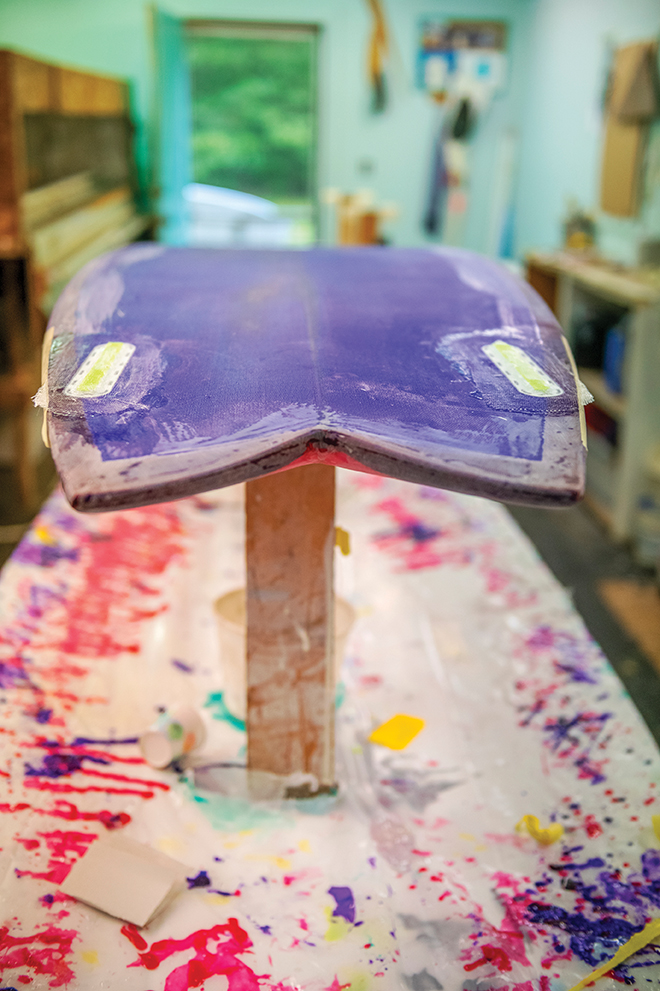
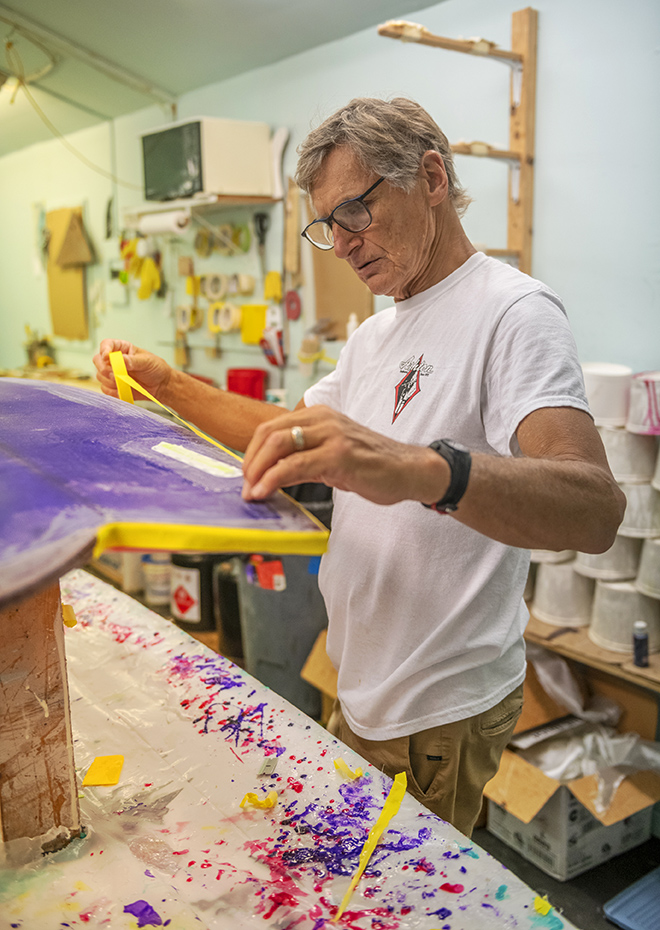
That immediately changed. Ashton began handcrafting custom surfboards by an artisan process that begins with plotting out measurements on foam: the wide point, nose and tail. He has about 100 templates, but every board is different in that it is designed specifically for the surfer. “The advantage of getting a custom board is that it should really be made for your weight, the shape you are in and your experience,” he said. “Custom boards are made for you.”
In many ways, Ashton is a tailor, assuring that every line and curve suits the wave rider. He roughs out the shape with tools and thoughtfully sands every piece. Then, he paints the foam — another important aspect of selecting a custom board. It allows surfers to express themselves with designs and words that speak to their styles, vibes and ways with the waves.
The painted boards are then coated with fiberglass, and longboards are glossed with resin and polished. Short boards are finished with a clear-coat speed spray. It’s a labor of love — a passion turned into a profession. A single board could be completed within a day and a half, but that might be pushing it. Usually, Ashton makes boards in batches of several at a time that are in various stages, so he’s in a continuous cycle of shaping, painting and finishing.
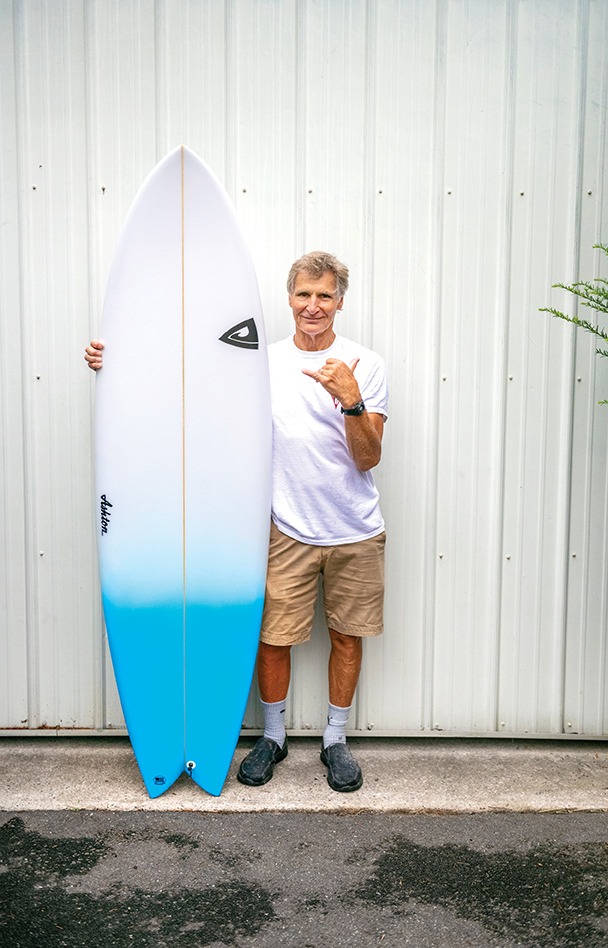
A portion of his business includes stock boards sold in surf shops along the East Coast. “Through that, people who have bought boards from shops will contact me to order a custom board,” he said.
From start to finish, the craft is practically innate to Ashton. He’s been doing it since age 15. Dialing back to the earliest days, when he was reworking old boards on the West Coast so that he could quickly get back on the waves, Ashton has since developed a loyal following of surfers who appreciate and seek out his work. CS