Nate Reister and the Burley Building Co.’s innovative and craftsmanship-focused approach to renovation and new construction is elevating standards across the region
Written by Kristen Hampshire | Photography by Grant L. Gursky
There is a better way, if you ask Burley Building Co.’s Nate Reister, to avoid chronic building and renovation pains, labor lags, supply chain backups and quality qualms. With his problem-solving mindset and eye for innovation, Reister leverages intelligent construction products and is constantly retooling to improve performance while staying rooted to generations-long craftsman values.
“We are thinking ahead in many ways,” says Reister, owner of the Berlin-based business that specializes in high-end timber frame homes with specialty millwork and the latest sustainable, energy-efficient products such as insulated concrete forms (ICF).
Reister was born and raised in Berlin and a great deal of his company’s work happens within close proximity of its Burley Street headquarters. He mentions that he could have named the business after himself, but his hope is that his venture will live on for his talented team to run one day.
Known for preserving historic homes and businesses in Reister’s hometown and in nearby communities, Burley Building Co. is a preferred partner of Maryland Historic Trust, having completed notable projects like the Calvin B. Taylor House Museum and a portfolio of work that includes replicating brickwork, stonework and leaded glass windows.
“We run their pig roast every year and the community gives back by taking part,” he says of the museum, relating how the Burley team stays close to its projects.

Nate Reister, left, and Adam Davis inside the new Berlin Beer Co.
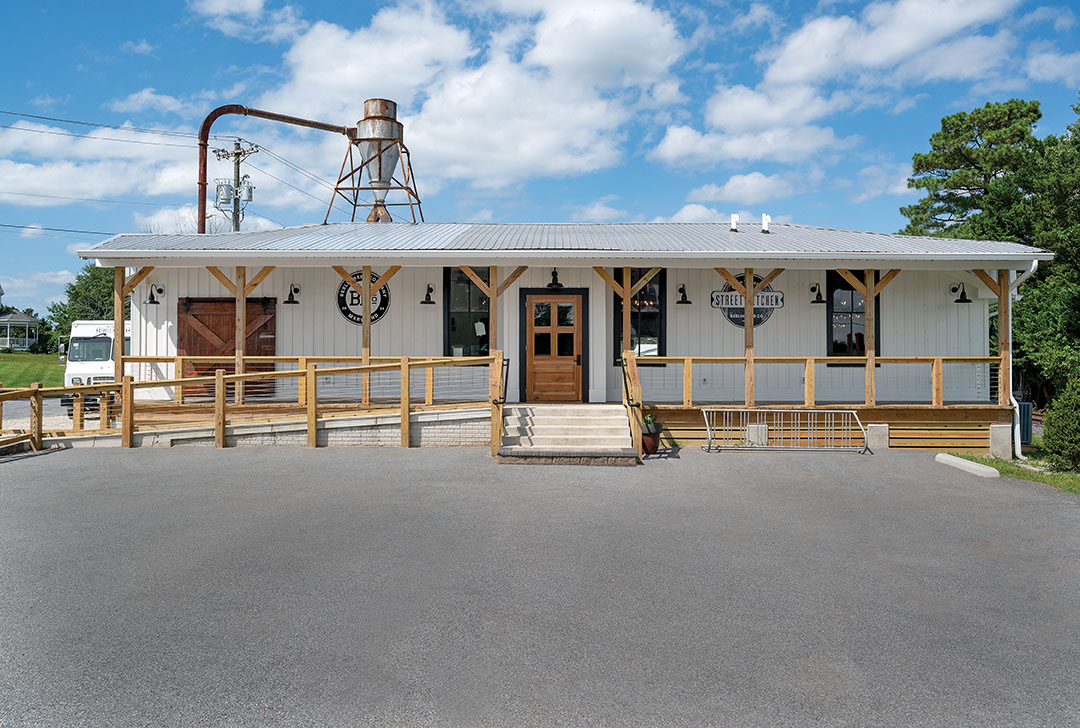
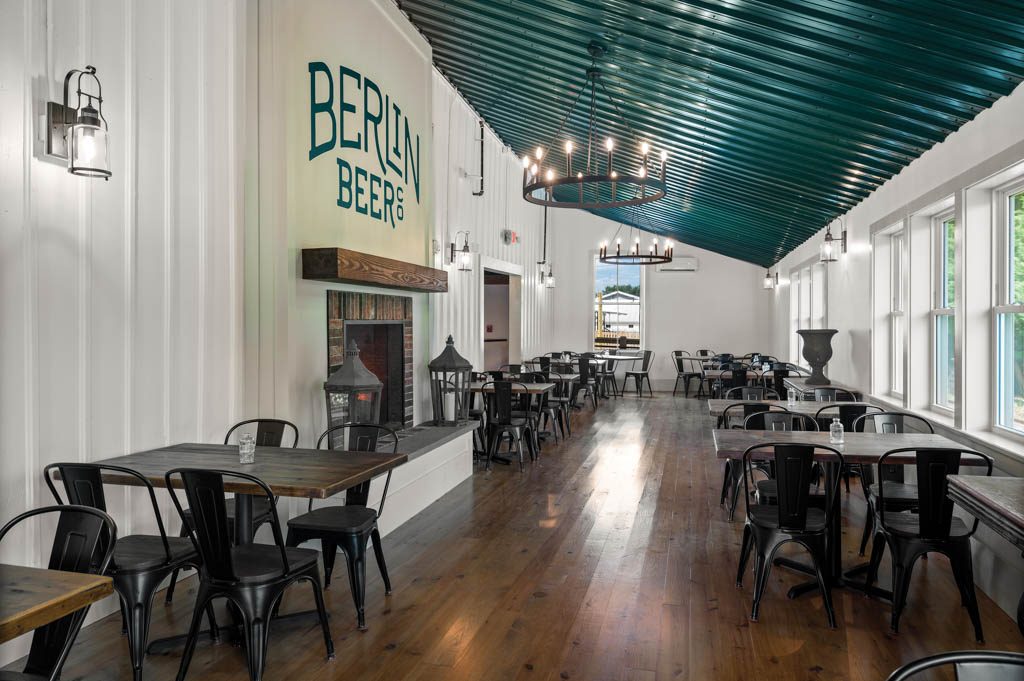
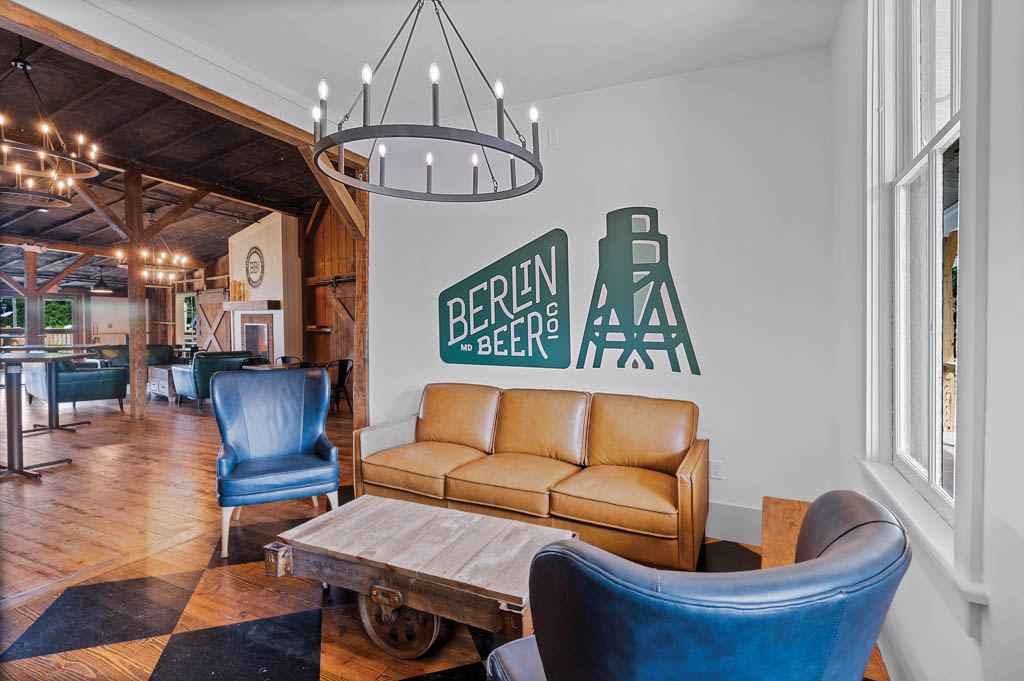
MODEL PRIORITIES
Burley Building Co. focuses on integrity, sustainability and artisan construction using advanced, energy-efficient materials.
Burley Building Co.’s most recent historic rebuild is the Berlin Beer Co. in the former Southern States Feed and Grain store, which included a reconstruction and substantial new addition. After marking its centennial, the building required modern structural integrity while maintaining its 100-year roots in what has been dubbed Maryland’s Coolest Small Town. “We love the historic nature of businesses and homes in this area, and we spend a lot of time restoring them,” says Reister.
Now, Burley Building Co. is nurturing an expanding, unique new home and commercial building model that prioritizes integrity, sustainability and artisan construction using advanced materials and even more energy-efficient buildings. Case in point: The R-value of ICF is 40 for a wall system compared to approximately R-25 for a standard home.
Reister says, “During the last year, we have been able to push down on the market and reduce the cost of framing while providing a superior product.”
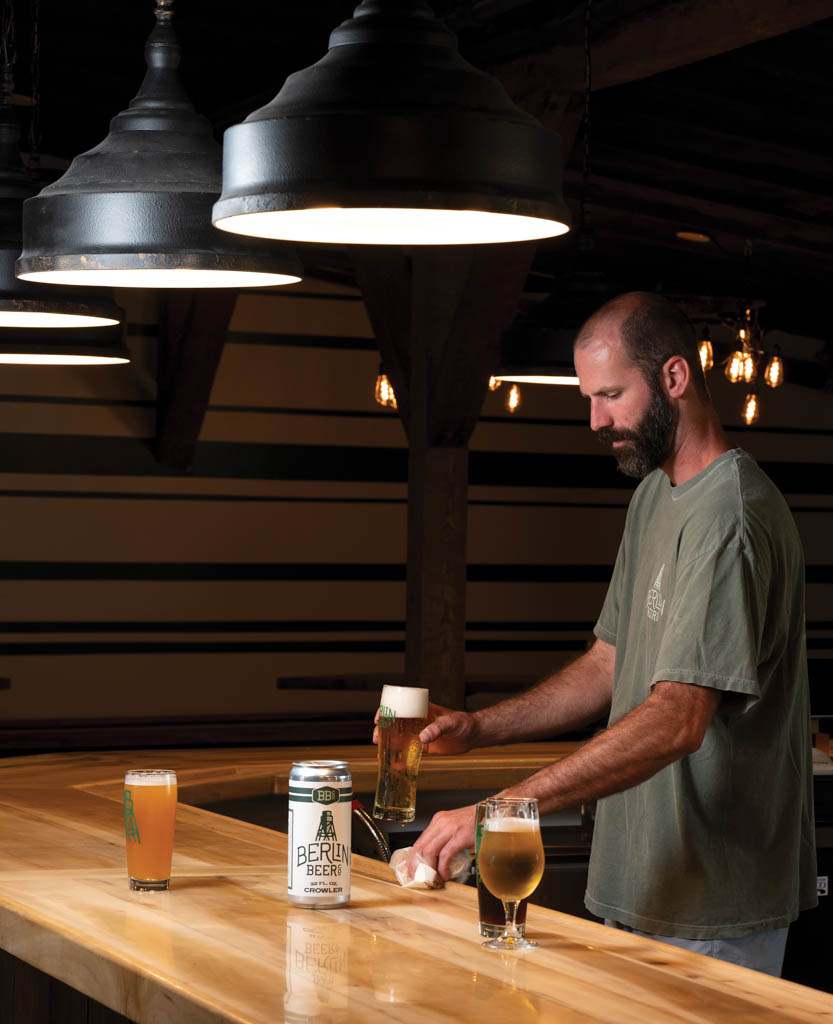
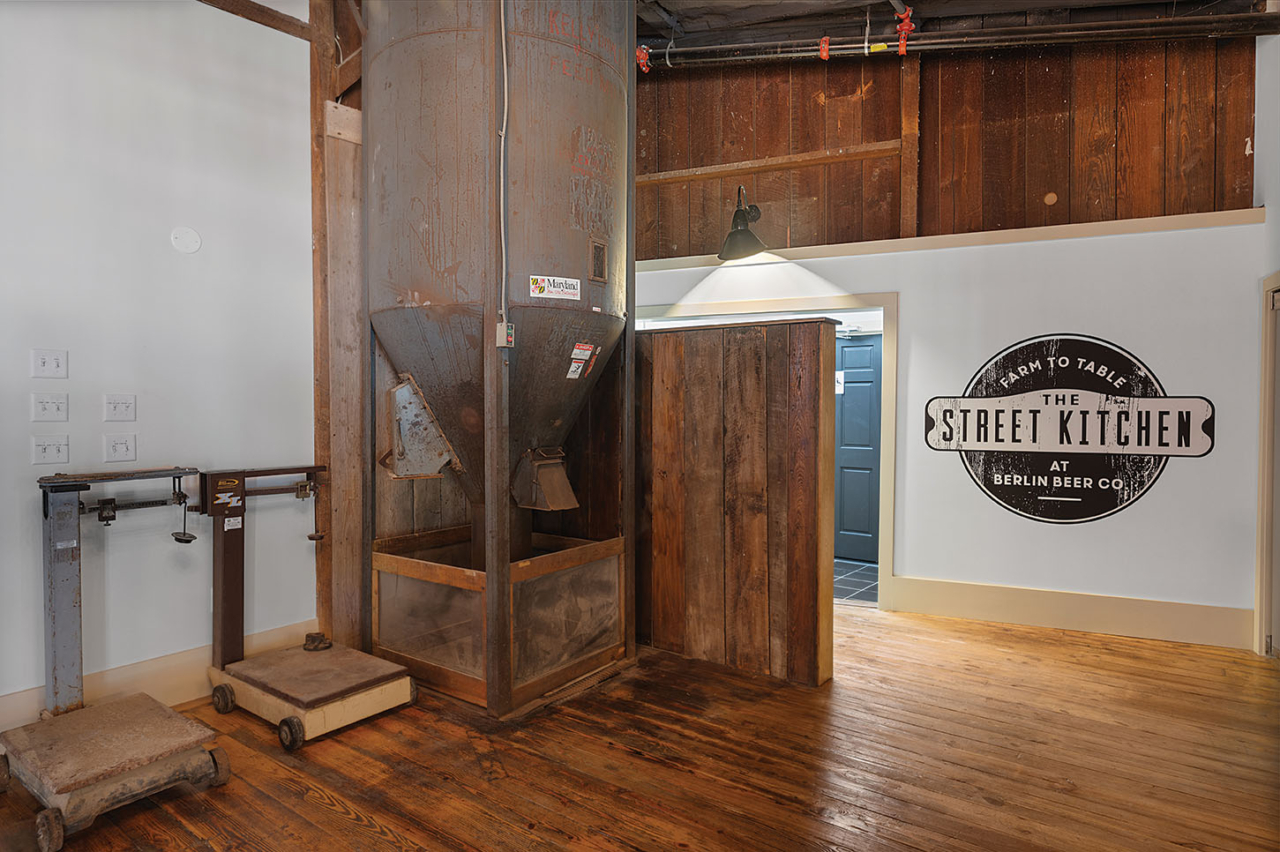
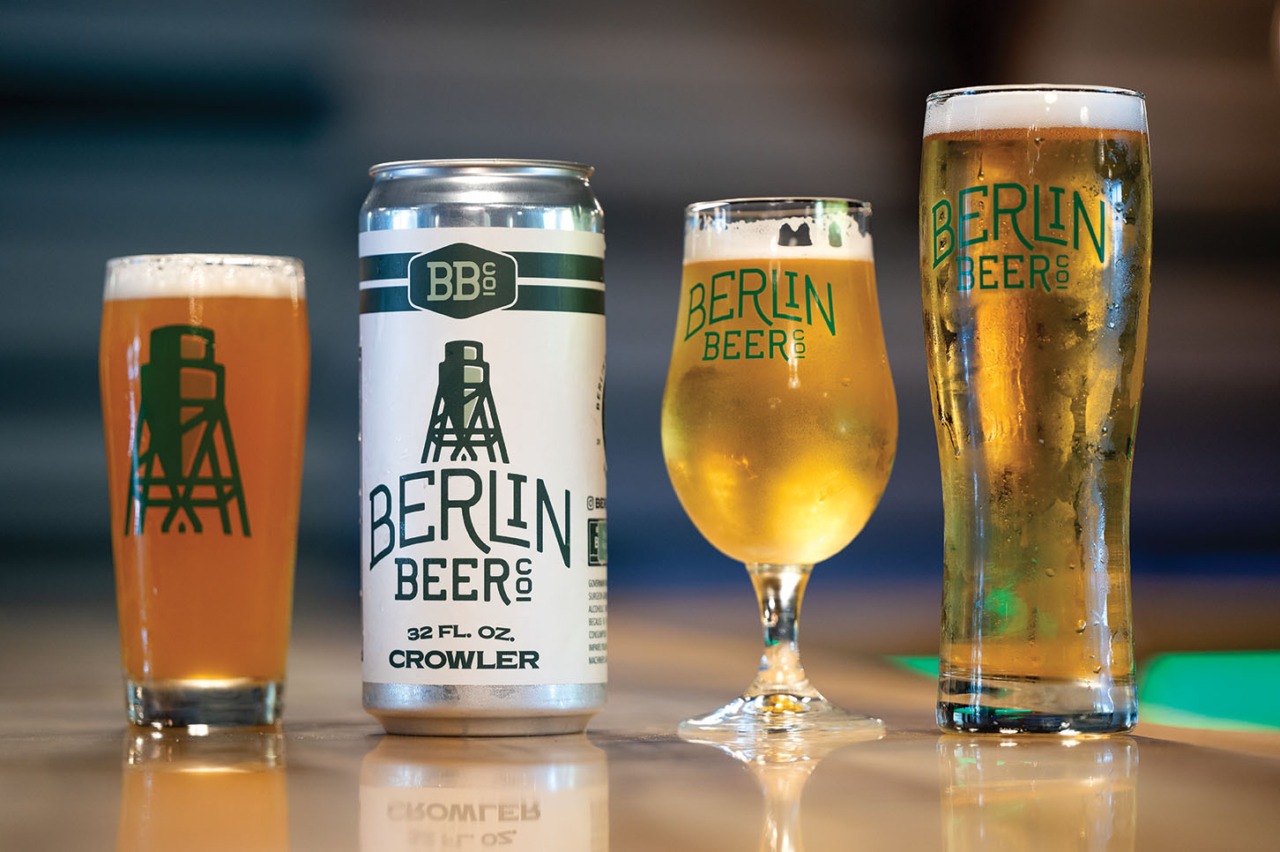
RESPECTING HISTORIC ROOTS
Burley Building Company’s recent transformation for Adam Davis and his Berlin Beer Co. property incorporates modern structural integrity while paying tribute to the structure’s 100-year-old bones.
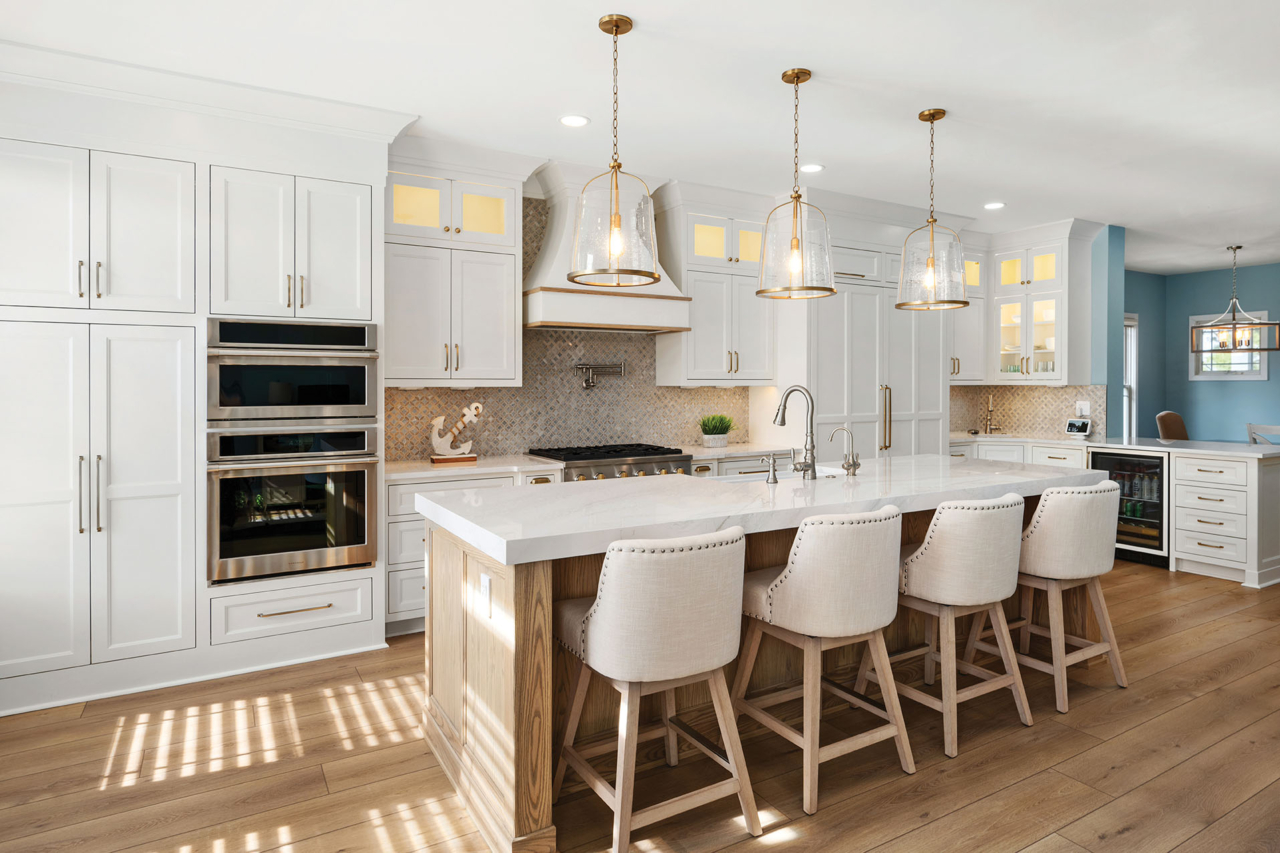
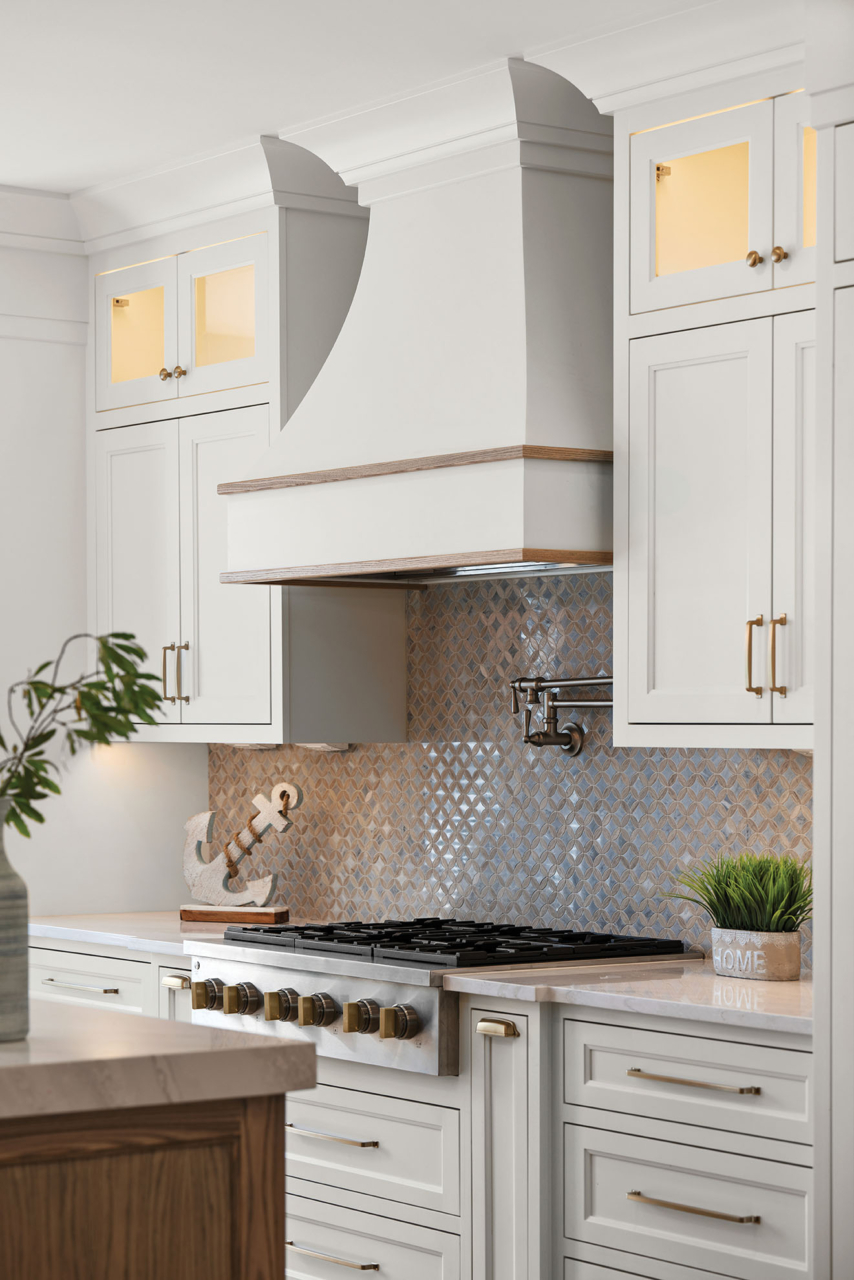
Photography by Svetlana Leahy
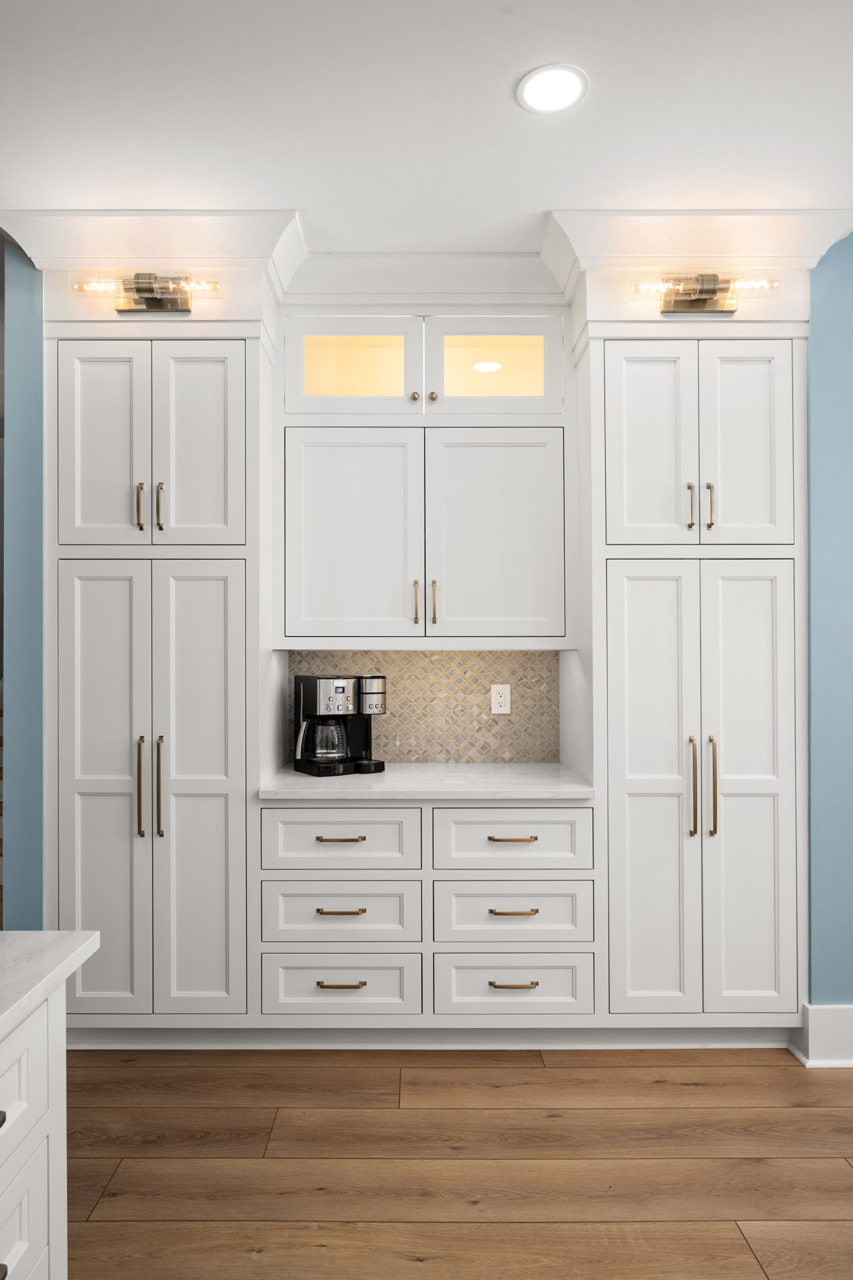
Farm-to-Table Construction
Burley Building Co. subscribes to a new-fashioned, old-time values way of providing custom cabinetry and millwork. The team constructs cabinets in its home workshop. Parts of the process are completed on site, resulting in a finish that Reister says is “unparalleled.”
“You can’t get the same look without building cabinets in place. All of the doors are fitted on site, and the product is sprayed in place so all paint is applied for a seamless look,” he says.
Such was the case with a recent luxury kitchen renovation project, in which the custom cabinetry includes a paper towel drawer in the island and an appliance barn with roll-out shelving equipped with electrical. A pantry space with peninsula bar seating features three stacked drawers, all inset, custom and with integrated lighting.
Burley Building Co. also mixes and color-matches its own stains—virtually unheard of in the industry, Reister says. “The Ash wood island stain was custom matched to the flooring using a new product called Gallery by Sherwin Williams,” Reister explains. To apply, the company uses a high-volume, low-pressure sprayer with an atomizer to achieve the gorgeous sheen.
The company has its own mill and excavating equipment. A portable mill allows Burley Building Co. to cut material on site. “We pick trees from local lots we are clearing for construction, take those trees and turn them into lumber that gets put into projects,” Reister say of the “farm-to-table model for building.”
“We are spending our resources locally,” he adds, “rather than relying on cabinet makers in another state or country to ship us product.”
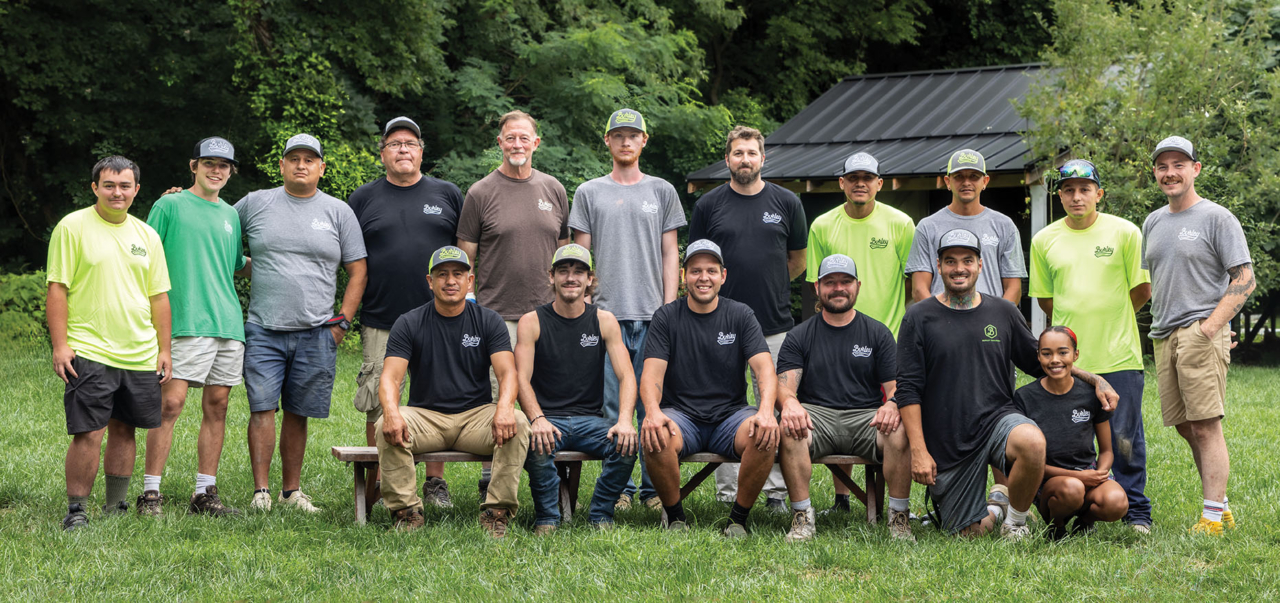
Photo by Krista Valliant
If You Build It…
Talent in the skilled trades is at a premium as is the demand for Burley Building Co.’s services. “In this market, many are complaining that they can’t find labor. But that has to be made,” says Reister, recognizing the need to proactively create a pipeline for the next generations of craftspeople. That’s why Reister’s company offers on-the-job training, mentorship and hands-on opportunities. He’s equally passionate about the company’s community outreach apprenticeship program that supports young people in the community and those looking to shift career gears into a fulfilling profession.
Because of this grow-your-own approach, Burley Building Co. is not dependent on subcontractors’ schedules and is a turnkey, full-service construction firm that manages projects from pouring the foundation to all of the finishing. “Our projects move more efficiently, and we can manage the quality and staff the entire time,” Reister relates.
With a consistent project lead on every job and a staff that stays on board with very little turnover, Burley clients receive the attention, high level of communication and superior outcomes they expect.
The detail-oriented millwork, custom-built cabinetry and structural features Burley Building Co. executes requires an innovative team inspired by ongoing professional development.
“It takes talent to do the type of work we’re introducing to the market,” Reister says.
He adds, “We want to build projects that are heirloom hand-me-downs for our clients’ kids—not a quick fix.” CS